It is assumed that a cellar or other room in which the temperature is fairly constant is available. Grinding, even polishing, might be done almost anywhere, but testing and figuring can be carried on only under conditions of uniform temperature.
Strokes
There are three motions that the optician must employ in order to preserve a surface of revolution on his mirror. First, the back-and-forth grinding stroke produces the curve. Second, the mirror must be rotated in order to produce this curve on all diameters. Third, the worker must walk around the barrel (or the tool must be rotated) in order to employ all diameters of the tool. While the directions of these last two motions are not important, they must not occur in unison, and for this reason it is perhaps safest if they are counter to each other. It is not necessary that any of the motions be performed with machine-like regularity, nor is it necessary to run oneself dizzy in their execution. Take six or eight strokes, rotate the mirror a trifle and shift to a new position where another six or eight strokes are taken, and so on.
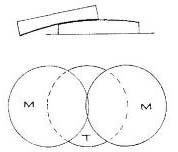
The lengths of the strokes at the disposal of the mirror maker are described with reference to the diameter of the mirror or tool. A full-diameter stroke is one in which the mirror travels a length of 6″; its center passes completely across the tool (Fig. 22). A one-half diameter stroke carries the mirror’s edges halfway in to the center of the tool, resulting in a travel of 3″. A one-third stroke carries the mirror’s edges 1″ past the edges of the tool. In using these strokes, the center of the mirror need not necessarily pass over diameters of the tool; much of the time, especially in the early grinding, and finally, in polishing to figure, chordal strokes are taken. But the length of the stroke — one-third or one-half, or some other length — is constant, whether performed diametrically, or over chords of the tool.
What Abrasive Does
If a grain of carborundum is placed between two disks of glass and one disk is slid over the other, a rolling action is imparted to the” grain. As its sharp corners impact the glass surfaces, fragments are chipped out, leaving pits. The carbo grain is itself broken down in size until effective grinding ceases. Increasing the rolling speed beyond a certain point merely increases the rate at which the grain is broken down; in fact, the chipping action on the glass is reduced. By increasing the pressure, however, the force of impact is increased, and larger chips are broken out of the glass.
When grinding a telescope mirror, if the carbo is too thickly applied, the separate grains are crowded together and are not free to roll. Instead, they are dragged en masse around the work, scratching and scoring as they go, until most of them have been pushed over the sides of the tool, and the rest worn down to a size where much of their efficiency is destroyed. It is a needless waste to apply the abrasive thickly, and the amount of grinding obtained will be small in proportion to the effort expended. Apply it thinly, and use plenty of pressure, with emphasis on pressure. Speed of stroke is also an important factor. Too rapid a stroke retards the hollowing-out process, and will flatten the edge zones of the mirror. Not more than 60 to 80 strokes per minute should be taken, calling a stroke, in this instance, the combined back-and-forth motion.
Working in this manner, glass can be removed rapidly, and with a minimum expenditure of elbow grease and carborundum. Just enough water should be used to keep the work wet. It may be necessary to add water from time to time as the abrasive breaks down, or as evaporation takes place. In rough grinding to curve, it is a waste of time to break each charge down fine. The purpose here is to remove glass, and when the sound of the coarse grinding ceases, a fresh charge should be added. The accumulation of “mud,” consisting of crushed abrasive, glass, and water, should be flushed from the surfaces occasionally; otherwise it may cushion the action of the carbo and slow up the grinding. This is important when working with the finer abrasives.
How the Curve Is Obtained
In order to produce a concave curve on the mirror blank, it is ground face down on top of another glass disk of the same diameter, called the tool. By using diametric strokes of a length that will bring the edge of the mirror almost to the center of the tool (approximately the full-diameter stroke), then, at the end of the stroke (Fig. 22, top), the pressure per unit area of surface, and hence the abrasion, is greatly increased at the edge of the tool and the center of the mirror. Thus, a greater amount of grinding takes place in these regions, with the result that the upper disk becomes concave, and the lower one convex. It is interesting to note that gravity alone would bring about this condition without the application of pressure, but at a much slower rate. On account of the long stroke used (a shorter one would also work, but the action would be slower) the surfaces are not in contact, and are not spherical. The reason for this is that the edge zones of the tool comprise an area that is approximately three times greater than that of the center zones of the mirror, so there is a proportionately greater removal of glass from the center of the mirror.They “fit” together somewhat as shown in Fig. 23, which is exaggerated to show the hyperboloidal figure of the mirror, and the oblate spheroidal figure of the tool. After the curve has reached the proper depth, the surfaces are then brought into contact and made spherical by wearing back the edges of the mirror. This is accomplished by means of a short stroke, in the early use of which the radius lengthens slightly. The reason for this is apparent from a study of the diagram.
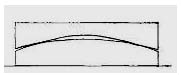
It does not matter that the pyrex mirror blank and the plate-glass tool are of unequal hardness, and of different expansion coefficients. A more-or-less uniform “fit” of surface is maintained, depending on the stroke used, the plate glass merely being worn away at a more rapid rate. And for all practical purposes, the expansion difference is insignificant.
The foregoing is an old and reliable method of obtaining the curve, but requires that an unnecessary amount of glass be removed. The worker should grind his mirror by the quicker, more conventional method about to be described.
We Go to Work
The upper edges of the tool must first be beveled all around for about 1/16″, with the coarse carborundum stone. The stone can be applied vigorously to the tool, and if a few small chips are knocked off, which is unlikely, it does not matter. Later, as the surface is ground down, causing the edge to become sharp again, the beveling should be repeated. This is important, so that during grinding chips will not break off and get between the disks, causing scratches.
Have the pail of water placed conveniently near. Shake a few drops of water on the barrel top, and place on it several sheets of newspaper, with sprinkles of water applied between them, and lay the tool in the center. The wet paper will provide enough adhesion to prevent the tool from sliding about during grinding.
![]()
|
Apply some No. 80 carborundum around the edge zones of the tool, as that is where the grinding will begin. Add water, and place the mirror on the tool so that its center is about ½” inside the edge. The one-third stroke is to be used, and grinding is to take place on chords of the tool, so that the center of the mirror is carried around the edge somewhat as in Fig. 24a. After taking six or eight chordal strokes (counting as one stroke the combined back-and-forth motion), rotate the mirror, shift to a new position, and work on another chord. The pressure should be applied over the center of the mirror (as shown in Fig. 24b), which should be sufficiently far in from the edge of the tool so that it will not teeter on the edge at the end of the stroke. If pressure were applied over the center of the tool, hollowing out would be slowed down considerably, although gravity would eventually do it for us.
After two or three trips around the barrel, wash and dry the mirror and try the template. When the curve in the small central area of the mirror seems right, take the next series of strokes on chords farther in on the tool. Spread the abrasive now over a wider zone, move the mirror in so that its center is about 1″ inside the edge of the tool, and grind as before. Apply plenty of pressure for quickest results.
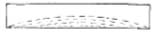
Frequent renewal of abrasive is necessary in the early stages. as much of it is pushed over the edge without being used. This residue can be scooped up later, placed in a jar of water and stirred, and the muddied water poured off. The unused abrasive at the bottom of the jar can then be reclaimed.
When the widened curve on the mirror fits the template, the mirror is moved inward another ½” or so, and ground until the extending curve again conforms to the template. If at any time the curve becomes too deep, move the mirror in considerably, and continue with the one-third strokes. The curve should extend to within 1/16″ of the edges of the mirror when it is grinding center over center on the tool; the curve will have been achieved by the steps shown in Fig. 25. Of course, we can hardly expect the mirror to be spherical. The concave surface will probably consist of a series of waves, with its general curve almost inevitably slightly hyperbolic, somewhat like the condition shown in Fig. 23. This must be corrected by continuing with the one-third stroke, working center over center until contact has been established.
As the abrasive grains lend to rolled in hollows and depressed zones, this stage of the work can be greatly facilitated if the disks are frequently separated and the carbo on both surfaces redistributed with the finger tips. At this stage, too, it is advantageous to prolong the time spent in grinding with each charge of No. 80 until it is thoroughly broken down. It may be observed, as the charges are ground down fine, that the mirror has a tendency to stick or grab whenever the grinding strokes bring the centers of the disks coincident. This sticking tendency occurs at the “edge zones, and is the suction effect of the central gap between mirror and tool. Repeated breaking down to a fine consistency of each charge of No. 80, together with frequent respreading of the abrasive, and use of the one-third or shorter stroke, is the quickest way to grind the edges back and bring the surfaces spherical. When contact is established, the curve should extend practically across the whole diameter of the mirror, there being enough of the original bevel present to prevent a sharp edge. A more exact determination of the radius should now be made.
Flush off the disks in the pail of water, and wash your hands as well. Deposit about 1/8 teaspoon of No. 400 carbo at the center of the tool, and puddle and spread it around the surface with the finger. Grind this down for about five minutes, stopping now and then to respread it. Then flush the mirror thoroughly and stand it, wet, on the testing rack. Using the window of the Foucault lamp, or any light source held alongside the eye, locate its reflection on the wet surface of the mirror. Move the light from side to side. If the reflection is seen to move in the same direction, you are inside the center of curvature of the mirror; if it moves in an opposite direction, you are beyond the center of curvature. When a position is found where the reflection just seems to appear, and from no determinate direction, as the light is moved from side to side, that is the center of curvature of the mirror’s surface, and the distance from mirror to eye is to be measured exactly. One half of this distance is the focal length, which it should be possible to determine within ½” at this stage.
The charge of No. 400 enables the surface to hold the water for a longer period. Even then you may have to interrupt the test to splash more water on the mirror. If the focal length is found to be about 49″, you are ready for No. 120, but if it is too long, continue with No. 80 until you bring it right. It is preferable to use the one-third stroke for this shortening, but if the radius is too long by several inches, a longer stroke will speed up the process, afterwhich some lime must be spent in again restoring contact. If the focal length is less than 49″, invert the positions of the disks, and grind with the tool on lop, using the one-third stroke. This stroke will lengthen the radius gradually, without deforming the figure. Use of a longer stroke, in any upside-down grinding, might flatten the mirror’s edge to an extent that it might refuse to polish later on, unless contact were thoroughly restored by means of a short stroke, used with the mirror on top.
About two hours of actual effort will be expended in achieving a curve of the proper depth, with the surfaces brought into contact. While the difference of a few inches in focal length either way is of no material consequence, we have decided on a length of 48″, and the worker may as well begin now to develop a skill in working to precision, and endeavor to arrive exactly at that focal length for the finished mirror.
If through prolonged grinding the edge of the mirror has become sharp, it should be carefully beveled with the fine carbo stone. In doing this, rest the mirror on the edge of the water pail, and bevel at a 45° angle, using the stone as though it were a file. Rotate the mirror slowly, and continue the filing stroke until the edge is smooth and rounded to the touch. A coarse stone can be used on the tool; because of the wider angle of its edge there is little danger of chipping. Beveling will in all likelihood have to be repeated during the fine grinding, or whenever the edges become sharp and there is danger of scratches from chipping.
How to Determine Contact
Numerous bubbles collect between the disks during the grinding, with the larger ones at the center. As the abrasive is broken down, the surfaces approach each other more and more closely, and the bubbles become smaller. If those at the center remain large, or if they are concentrated locally in that area, they indicate a gap between the disks there. In this event, when a charge of abrasive has been broken down very fine, so that at the edges the surfaces may be actually abrading each other, suction caused by the central gap will make the disks stick and cling. Upon separating the disks, it will be found that the abrasive around the edges is fine to the touch, while comparatively large grains still remain at the center. When the rough-ground surfaces fit at every point, that is, when they are spherical, they will pass back and forth over each other evenly during grinding and no clinging will occur. The means just described for determining contact are entirely satisfactory in the coarse-grinding stages, and in fact are all the criteria needed to carry one safely through fine grinding. But the mirror maker may feel more confident if he can have visible confirmation of what may be, in the case of the inexperienced, sheer guesswork. There are two ways of obtaining a visual check on the sphericity of the curve.
The first is a simple application of the axiom that only flat or spherical surfaces can be rubbed against each other and make contact at every point. Wash and dry both tool and mirror and, with the palm of the hand or under side of the forearm, brush off any lint that may be left on the surfaces by the towel. Now short-stroke the mirror on the tool, going through the motions of grinding for about half a minute. On separating the disks, a fine dust, consisting of powdered glass, will be seen in those areas where the surface has been abraded. Or if not clearly visible, the dust can be found and picked up on the tip of the finger.
The second method is a matter of variable reflection. We know that from a polished glass surfaceabout four per cent of light of normal (perpendicular) incidence is reflected. As the surface is tilted, increasing the angle of incidence (the angle made with the normal), the percentage of light reflected increases, slowly at first, and amounts to total reflection as the angle of incidence approaches 90°. On an incompletely polished surface the amount of reflected light is lessened, and on a ground surface it may be nil (barring diffusion) except for very oblique rays, depending on the fineness of the grinding. And this is where use of a charge of No. 400 at the termination of work with No. 80, and the subsequent less-fine grades also, is beneficial.
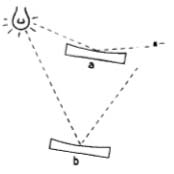
Hold the clean, dry mirror face up, somewhat below a line between the eye and an unfrosted light bulb, as in Fig. 26a. A reflection of the filament will be seen on its surface. Now slowly lower the mirror, centering the reflection, which will become reddish or copper colored and fainter as the reflection angle is decreased. When it is quite dim, stop, and slowly slide the mirror to the right or left, allowing the reflection to pass across a radius, and off the edge. If the mirror is spherical, there should be just a slight and gradual diminution of the reflection from center to edge. In the event of imperfect contact (lack of sphericity), high zones will be revealed by a brighter reflection, and low zones by a dimming of the reflection. Slight differences can be tolerated, but any abrupt change in the quality of the reflection should be remedied before proceeding to a finer grade. In making this analysis while working on No. 80, the mirror may have to be held as at a, and in the final stage of fine grinding, as at b, Fig. 26.
Cleaning Up
Before going to fine grinding, or before going from any grade to a finer one, a thorough cleaning up should take place, so that there will be no possibility for a coarser grade to get near the mirror again. Otherwise, a grain or two of a coarser grade may find its way between the disks and chip wide swaths in the surface of the mirror. And, when polishing, even the finest grain of carbo on the lap will cause unsightly scratches.
The bench top, water bottle, spoon, template, flashlight, water pail, apron, and anything on which loose abrasive may lie should be dusted, wiped, or flushed. It is not necessary to remove every last carbo grain from the water pail each time it is flushed out. Well-behaved grains will remain at the bottom where they can do no harm. Flush the handle and rim, however, and keep clean water in the pail.
A skilled worker, abrasive-conscious and familiar with the routine, can bring a mirror through to the polishing stage without leaving his bench, save for checking the curve, pausing only long enough to change papers and to flush his hands and the disks. If you have not contaminated anything with carbo, no time need later be lost in an elaborate cleaning up.
Fine Grinding
The mirror maker has his choice of three ways of performing the fine grinding. The mirror may be ground on top of the tool, accompanied by a shortening of the radius; or the mirror may be placed on bottom with the tool on top, in which case the radius will lengthen; or the positions of the disks may be alternated, either with each charge of abrasive, or for half of the charges of each grade, and a constant radius can be maintained. By these means the worker has control of the focal length, which should be about 481/4″ when fine grinding is completed. Polishing will usually reduce this by 1/8″ to 1/4″.
As to stroke length, the one-third stroke is the longest that can be used without deforming the surfaces. It will at the same time produce the greatest change in radius, amounting, if used continuously throughout fine grinding in the same positions, to 3″ or 4″ or more. A shorter stroke, say about ½”in length, will produce a minimum of change, perhaps of only an inch or two. An advantage in alternating the disks is that greater freedom of movement is had, and equal abrasion is accorded to the edge of the mirror, where the least action takes place in the usual grinding-on-top. At no time should a rapid stroke be used in an effort to speed up the work, as this will almost certainly result in flattening the edge of the mirror. In any upside-down grinding, not more than a one-third stroke should be used, for a similar reason, except in a deliberate attempt to lengthen the radius radically. As he knows his focal length to a very close approximation, the worker can now select the stroke and method to be used with No. 120.
About six to 10 charges of each grade of carborundum, depending on the pressure used, should be thoroughly ground down, but for the beginner it is recommended that not less than eight charges be used. About five minutes is enough for each charge, but if one is unable to maintain heavy pressure a charge should be worked for a longer period. The purpose of each successively finer grade is to remove the pits left by the preceding grade, and to be assured of this not less than 40 minutes should be spent on each.
Before leaving No. 120, work the last charge down well, then follow with a charge of No. 400 (worked with the mirror on top), and again test for focal length. This time we have a surface which, when wet, will be capable of producing a fairly sharp image of the window of the Foucault lamp. Use a piece of ground glass, held before the eye, to pick up the reflection from the mirror, and adjust the lamp until it and the sharply focused image of the window are equally distant from the mirror. Half this distance is the exact focal length, which should be about 49″ at this stage. If it is found that a slight correction must be made, of an inch or two, it should be done on this grade. Any greater correction should be made with No. 80. It may be more convenient to use a piece of bright tin, rather than the ground glass, in picking up the reflection, as the worker may then stand closer to the mirror and can more quickly reach and adjust the rack. The eye has to be placed in back of the ground glass, but a more critical determination of sharpest focus can be made with it.
When working with the mirror on top and using a short stroke, there may occur a slight lengthening, rather than the expected shortening of the radius. It would have been difficult and impractical to bring the surfaces into exact contact with No. 80 on account of the coarse grain size, and a thin gap may have persisted at the center. But as finer grades are used and broken down, the surfaces approach each other more closely, and a slight lengthening of the radius may thus take place through the wearing back of the edge zones of the mirror. After complete contact is established, however, the radius will begin to shorten.
The focal length now being quite exactly known, the worker can proceed with confidence. The radius can again be checked upon the completion of each grade. As finer abrasives are used, the quantity for a single charge should be reduced; for example, just a pinch of emery No. 305 will suffice. In using carbo No. 400 and finer grades, the abrasive should be deposited at the center of the tool (or mirror, if it is on bottom), a few drops of water added, and the mixture puddled and spread over the surface with the finger tip. After each of these finer charges is thoroughly worked down, the surfaces should be flushed clean of mud before applying the next charge. Faster action is obtained in this way. With the last two grades, the tiny bubbles that have always been present between the surfaces should be eliminated before grinding starts. This is done by moving the mirror out over the tool, slowly rotating it the while; the bubbles will disappear over the edge, leaving nothing but a thin film of water and abrasive between the disks. Only five charges of No. 305 need be used, but the last one should be worked out for about 15 minutes, with the mirror on top, adding water when necessary. It should be possible to read 12-point type, held at a distance of several inches, through a mirror ready for polishing.
If the tool is of the recommended thickness, pressure can be used throughout the fine grinding, but beware of the disks sticking together in the final stages. Evaporation may cause them to stick, so if it is necessary to pause for a moment, the disks should be separated. Otherwise, keep them moving at all times, and if there is a suggestion of stickiness, due to evaporation, separate them immediately. As previously explained, suction from lack of contact at the center will also cause them to stick. If this occurs, use a carpenter’s wooden clamps to separate them, or wedge the tool on a bench, hold a block of wood against the side of the mirror, and free it with a sharp blow of a hammer.
Examining for Pits
Hold the clean, dry mirror before a light, and with the magnifier examine the texture of the surface at the center. The pitted surface should appear uniform with no inter-mingling of large pits. Compare it with an area out near the edge. There should be the same uniformity of surface appearance, indicating that grinding is going on evenly. It may be helpful to cut up four small squares of plate glass and grind them together in this fashion: 1 and 2 with No. 400; 2 and 3 with No. 220; and 3 and 4 with No. 120. The worker is thus provided with comparison surfaces of these grades, but the same texture should not be looked for, as it should be remembered that there is a difference in the hardness of pyrex and plate glass. Prevention here is the best cure. If the worker thoroughly grinds down eight charges of each grade of abrasive, with pressure continuously applied, he need waste no time looking for pits.